Heating and cooling are fundamental aspects of processing industrial minerals and chemicals into market-ready products and materials.
While the available technologies for drying, heating and cooling bulk solids can make deciding on a given approach challenging, processors often come to rely on rotary drum technology for the many benefits it can offer.
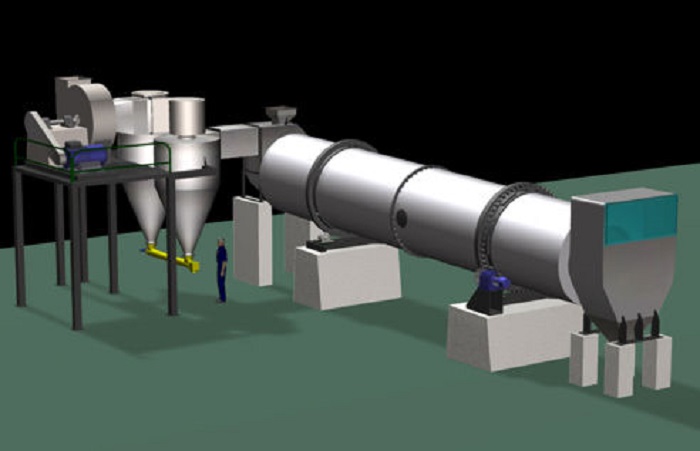
Rotary drums are unbelievably versatile in their ability to process materials. From scrubbing ores to coating fertiliser products, these drums will accomplish variety of process objectives. They conjointly offer important chance for customizing the drum around the specific demands of the intended application. No matter what they’re tasked with accomplishing, however, they all rely on a similar basic technology: a rotating drum.
The rotary drum consists of a large, rotating cylinder resting on a stationary base and situated between housings on each end that connect the drum to the surrounding process. The stationary base is in part made up of a drive assembly, which powers the unit to allow rotation on the base.
Material is fed into one end of the drum, that is set on a small angle thus gravity will assist in moving material through the drum, whereas additionally achieving the required retention time. Material tumbles through the drum and is exposed to the process medium (heat, binder, liquid additives, chilled air, etc.) to succeed in the required objective, at that point it discharges from the drum and moves on to downstream process.
When it comes specifically to drying, cooling and heating material, rotary drums are customized as follows:
Drying (rotary dryers)
Rotary drums used for drying are referred to as rotary dryers. They will be used as a pre-production step, helping to organize material for subsequent process, or as a post-production step, finishing material into its final dried form. They’re widely utilized in the process and production of minerals, fertilizers, aggregates, process by-products, pulp and paper residuals, salts, sugars and etc.
Cooling (rotary coolers)
Rotary drums used for cooling are stated as rotary coolers. Rotary coolers are utilized to reduce the temperature of incoming material or product in order that it will be handled without risk to downstream employees or equipment. Cooling additionally helps to stop caking and discourage mould or bacterial growth in the product during transport, storage or shelf life. Rotary coolers are often utilized as a finishing step in fertiliser production.
Heating (rotary kilns)
Rotary kilns aren’t that different from rotary dryers; the distinction is that they generally operate at much higher temperatures, as they’re supposed to cause a physical change or chemical reaction within the material being processed. As such, their applications are numerous, falling under specialty chemicals, mineral concentrates, roofing granules, process by-products and industrial wastes, adsorbents, technical ceramics and etc.
Benefits of utilizing rotary drums for process heating and cooling
Rotary drum technology offers several benefits in a process setting and as such, has become a favoured approach to processing in a number of industries ranging from chemicals to minerals, and everything in between. Rotary drums are often recognized for the following advantages:
- High throughput
- Easy to use
- Established and supported technology
- Robust design and build
- Extremely reliable
- Largely insensitive
- Tumbling action
- Efficient
Conclusion
While heating and cooling need totally different approaches to process bulk solids, each objectives, along with many more, can be met with the variety of rotary drum technology.
Rotary drums provide various benefits in a process setting, not the least of which is their sturdy build, reliableness and high throughput. They additionally permit plant managers to streamline operations by utilizing a single technology to carry out many objectives in a production plant.
We at KERONE have a team of experts to help you with your need for Rotary Dryers in various products range from our wide experience.