Natural diamonds form deep underground, about 177 to 241 km below the surface. Pressures at this depth can reach nearly 50,000 atm. (One atmosphere, or “atm,” is similar to the air pressure at sea-level). Temperatures will vary from 900º to 1,300º C. These intense conditions compress carbon into its most compact type, making diamonds in magma. Ancient volcanic explosions brought these diamonds to the surface, through the formation of rocks known as kimberlite.
There are 2 main lab-grown diamond production methods: the high pressure/high temperature method (HPHT) and chemical vapor deposition (CVD). Each ways are usually used, however CVD is becoming more popular for manufacturing gem-quality artificial diamonds for jewelry. HPHT is utilized more usually to make artificial diamonds for industrial use.
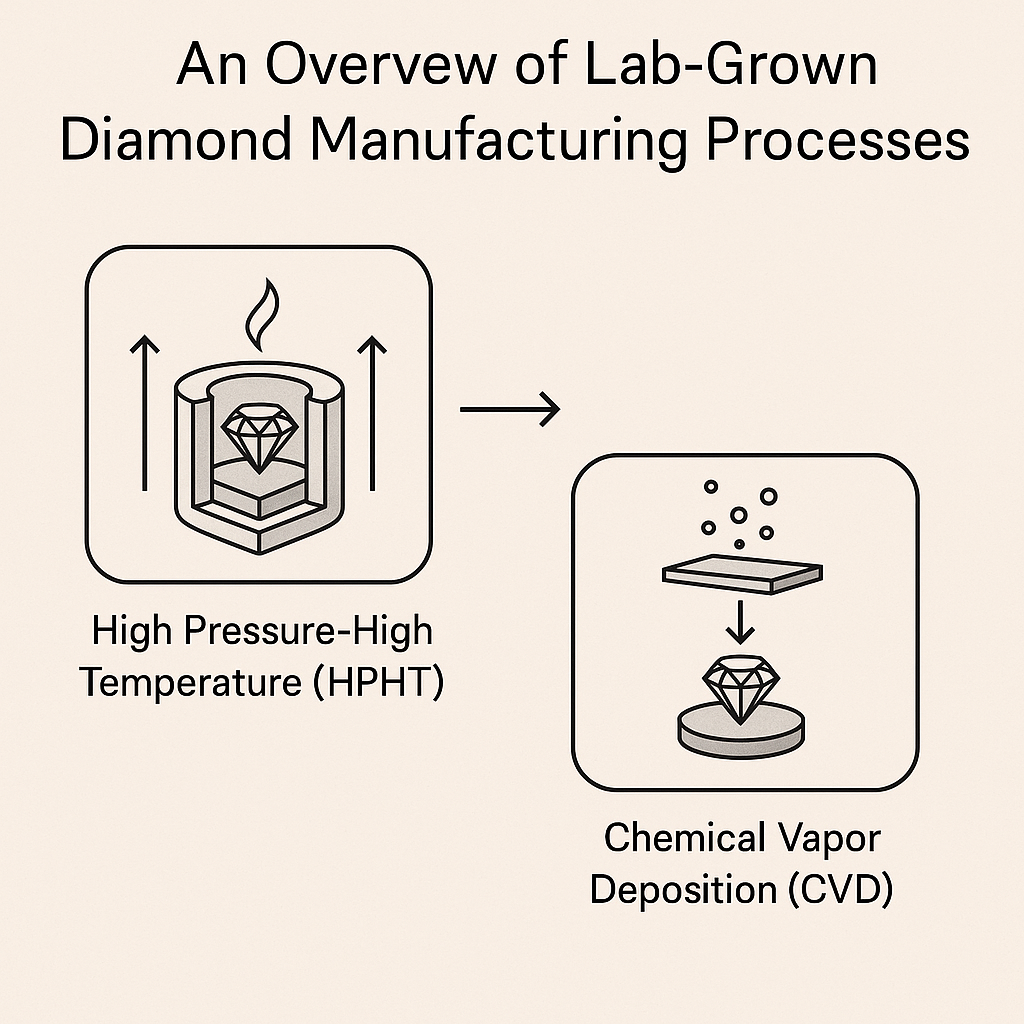
Both HPHT and CVD manufacture diamonds with a similar optical, physical, and chemical properties as natural diamonds. However, these laboratory processes do leave some telltale signs that gemologists will identify by close examination.
In rough crystal type, the variations are more promptly discernible. Natural diamonds form with eight sides of growth, forming an octahedral crystal shape. On the other hand, HPHT diamonds form in a cuboctahedron shape with fourteen directions of growth. CVD diamonds form in a cubic shape with one direction of growth. Of course, all diamond crystals form in the isometric system, and all these shapes fall among this method.
Developed in the 1950s, HPHT was the first method developed for diamond synthesis.
The process begins by placing into a press a capsule containing a carbon starting material, a mixture of metals called a metal flux, and a small diamond seed. The carbon starting material used in this process is usually graphite, a common mineral composed of pure carbon.
The capsule is then heated to temperatures of 1,300º to 1,600º C and pressed to pressures up to 59,200 atm. This dissolves the carbon source into the metal flux. The makeup of the metal flux varies, but often includes a mixture of iron, nickel, and cobalt, which helps reduce the temperature needed for diamond formation. The dissolved carbon source can then pass through the molten metal mixture to crystallize around the diamond seed, forming a lab-grown diamond.
The HPHT process can take from hours to weeks, depending on the desired size and quality of the stones.
There are three types of presses commonly used in HPHT diamond synthesis: belt, cubic, and split-sphere (also known as BARS).
The belt press was the first press used in lab-grown diamond production. With various advancements and alterations, it remains in use today. The belt press uses two anvils to apply pressure to the capsule from above and below.
The belt press led to the development of the cubic press. A cubic press functions like a belt press however uses six anvils, so as to work with larger, cubic materials. Although a cubic press will apply larger pressure than a belt press, technicians can’t scale it the same way as a belt press. As a result, cubic presses aren’t used as usually as belt presses.
The split-sphere press uses eight outer anvils and 6 smaller inner anvils, so as to maximise pressure on the capsule. The cylindrical capsule is then placed into an oil-filled barrel to accelerate heat transfer. This helps achieve higher temperatures at a far quicker rate.
Most HPHT diamonds can undergo more heat treatments when they come out of the presses. These treatments can improve their color and clarity and might even produce fancy colored diamonds. As an example, heat treatments with boron will turn HPHT diamonds blue. Heat treatments with nickel will turn HPHT diamonds green.
Radiation treatments can also create pink and red colors in HPHT diamonds.
The CVD method begins by filling a chamber with a mixture of gasses, including carbon, hydrogen, and oxygen. Next, a substrate is added to the chamber, typically a thin sliver of diamond seed, although graphite also can be used. The chamber is then heated to temperatures of 800º to 900º C, utilizing microwaves, lasers, or a hot filament. The energy from the heat source causes the carbon to precipitate out of the gaseous mixture and stick with the substrate that begins to crystalize into a diamond.
Technicians must stop the CVD process frequently, so they can remove any graphite that crystalizes around the diamond.
CVD can take from days and weeks, depending on the desired size and quality of the stones. However, dozens of stones can be grown at the same time.
Most CVD diamonds come out of the chamber with brown or yellow colors. In order to be sold as white or colorless diamonds, these stones must undergo heat treatment. After formation, CVD diamonds can also receive treatments to create fancy pink or red color.
Adding boron or nitrogen into the chamber during formation can also create fancy colored blue or yellow colors in CVD diamonds.
Lab-grown fancy colored diamonds, whether produced via HPHT or CVD, are much more affordable than their natural counterparts.
At Kerone, innovation meets precision. Our state-of-the-art solutions for lab-grown diamond manufacturing, including High Pressure High Temperature (HPHT) and Chemical Vapor Deposition (CVD) technologies, are built to deliver exceptional quality, efficiency, and sustainability. With a commitment to excellence and technological leadership, we empower diamond producers with reliable, scalable, and energy-efficient systems.