For a Manufacturer of proprietary granular chemical product, long production times and inconsistent drying times were the problems. A circular fluid-bed dryer/screener system from KERONE provided the solutions.
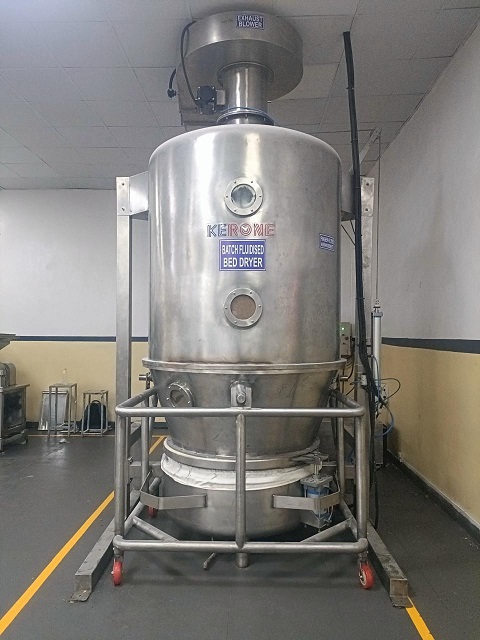
With a circular fluid bed dryer/screener, converted material from storage containers is fed into the top inlet of the dryer by a bucket elevator. Within the fluid-bed chamber, the material vibrates on a circular screen among a rising column of 120oF (49oC) air created by an upstream heater/blower ducted into the bottom of the chamber. The continuous air flow and vibration that is induced by 2 vibratory motors and spring suspension separate and fluidize individual particles, maximising surface area and drying efficiency. The vibratory action also causes material to travel from the middle of the screen to a discharge spout at the screen’s outer boundary in controlled spiral pathways on a first-in-first-out basis, ultimately discharging dried material into the top-center inlet of the circular vibratory screener.
An imbalanced-weight gyratory motor positioned beneath the screener chamber vibrates two screening decks. Oversize particles travel in controlled spiral pathways from the center of the screen to a spout at the screen’s periphery, where they are discharged for reprocessing.
On-size and undersized particles pass rapidly through the top screen to a bowl-shaped feed tray that directs them to the center of the second screen. On-size particles travel in controlled spiral pathways to a spout at the screen’s periphery, where they are discharged, while undersize material passes through the screen onto an integral metal chute that discharges it through a third spout for reprocessing.
Skid-mounted, turnkey dryer-screener system configures a 48″ fluid-bed dryer and two-deck circular vibratory screener in series to dry proprietary granular chemical product while removing undersize and oversize particles.
Putting It to Work
For the producer of proprietary granular chemical product, the circular fluid-bed dryer suited the product. The product consists of a granular carrier material, filler material and a vigorous ingredient. In the new production method, the granular carrier is screened into a slim size range utilizing Kason’s 48″ (1,220 mm) DIA., two-deck Vibroscreen circular vibratory screener. Once the carrier material is sorted, the filler material and active ingredient are added, and the batch undergoes a proprietary conversion process.
From there, it transfers to a 48″ DIA. circular fluid bed dryer that reduces the moisture content of the converted material to less than one % at 120oF. When the batch is dried, it’s discharged into the integral 48″ two-deck Vibroscreen separator that removes agglomerates and fines. The separator discharges the product into bulk bags at a rate of 2,000 lb/hr (907 kg/hr).
Any increase in the ratio of active ingredient to carrier and filler increases the occurrence of agglomeration, so the company monitors the ratio of agglomerates to on-size material to detect whether any method variation has affected distribution of the active ingredient.
Because the drying-screening portion of the general method operates offline, it can also be used to dry raw materials containing excess moisture or to dry other bulk products manufactured by the company. In anticipation of wide-ranging drying applications, the system was engineered to operate at temperatures higher than that needed to dry the proprietary chemical.
Kerone Fluid Bed Dryer is engineered for precision and performance in granular chemical manufacturing. Whether you’re drying fertilizers, catalysts, or specialty chemicals — experience uniform moisture removal, energy efficiency, and scalable results.