Imagine processing three whole tons of coconut shells on an everyday. Now imagine processing three tons per hour. That’s what you’ll be able to do with among the finest coconut shell charcoal making machines. These machines turn the shells into charcoal, and you’ll depend upon high cost performance and potency. This equipment is popular in a variety of countries, particularly needless to mention in geographical locations where tons of coconuts are grown. In the market, KERONE is a coconut shell charcoal producing machine manufacturer that has several projects.
What’s good with regard to the coconut shell charcoal manufacturing machines would be that the shells are usually waste. Why waste something which will be transformed into something which can be sold? You’ll sell that charcoal permanently money, and it originates from something that was going to be thrown away. It’s all about the procedure for carbonisation.
Charcoal Production from Coconut Shell
Process: Carbonization / Pyrolysis
- Step 1: Drying – Moisture in the shells is removed to ensure efficient carbonization.
- Step 2: Pyrolysis – The shells are heated in an oxygen-limited environment at ~400–600°C.
- Step 3: Charcoal Collection – Solid carbon (charcoal) is collected as the main product.
Outputs:
Charcoal – High calorific value, used for fuel, filtration, etc.
- Byproducts – Syngas, tar, and wood vinegar (can be captured and utilized).
You are able to process a lot more than charcoal, too. In reality, these biomass pyrolysis plants will look after straw, wood, sewage sludge as well as different raw materials and turn them into charcoal too. Are you aware that the charcoal made from coconut shells will be converted into biogas through reprocessing?
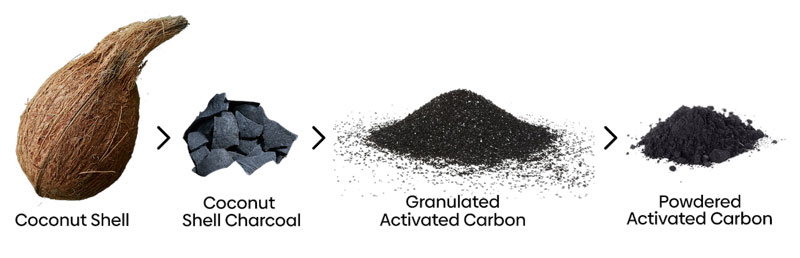
While raw coconut shells are not ideal for anaerobic digestion (due to lignin), shell dust, shell processing residue, or liquid byproducts from pyrolysis can be processed into biogas.
Option A: Pre-treated Shell Powder
- Pre-treatment – Mechanical + chemical (acid/alkali) to break lignin.
- Anaerobic Digestion – Microorganisms break down organics in absence of oxygen.
- Gas Collection – Mainly methane (CH₄) and carbon dioxide (CO₂).
Option B: Syngas Conversion
- The gaseous byproducts of pyrolysis can be cleaned and converted to:
- Biogas (methane-rich)
- Or directly used as fuel gas
It is possible to trust this type of machine to operate endlessly for round the clock straight. It comes with an auto feeder function, and you’ll also configure the appliance with what’s known as water cool slag-out. These machines are also meant to be designed to enhance the utilization of heat to be able to help conserve energy.
You need to meet environmental standards of course, and in order to do that, it is advisable to ensure that your charcoal making machine features a de-dusting system. You can reduce approximately 95 percent from the combustible waste, and you find yourself with good-quality products. The charcoal you get in the machine is composed of 90= percent carbon.
Some of the charcoal making machines don’t process around 3 a lot of coconut shells as well as other raw materials an hour. You should take into account the capacity in the machine you require. How much coconut shells come using your processing plant? The fact that this particular machine can run continuously is likewise gonna enter in to play.
You’re going to need to look at the model, hourly feeding capability, operating technique, raw materials, reactor size, pattern, heating materials, total power, floor area, operating pressure, cooling method and life-span. Those are essential factors to contemplate beyond doubt whereas you’re investing in a charcoal making machine.
The length of time would you expect a charcoal manufacturing machine to last? You’re planning to need to have a look at manufacturers to see what machines they have to offer. You’re planning to need to concentrate on the specs and has mentioned, and you can make a decision concerning what machine to acquire. You’ll be recycling coconut shells into charcoal, and you’ll even change it into biogas.